Local sourcing of sand
Sand for flat glass production must meet stringent properties in grain size and chemical composition. Therefore, sands from riverbeds, sea beaches or marine sandbanks are not suitable as they do not meet those conditions. Only silica sand extracted from fossil deposits (sand pits) or from the crushing of sandstones (quarries) can be used to produce flat glass.
Extracted silica sand comes in various qualities (different thickness, grain size, chemistry, contamination by clay, feldspar, organic material, dense mineral, etc..) and must be processed and cleaned to obtain the high quality needed for flat glass production. AGC Glass Europe performed an extensive review of its sand supplies in order to identify the ‘just good enough’ sands which present minimal expected quality requirements without excessive processing. A challenging review, as unstable quality and yield losses have a deleterious impact on furnace output, and thus on the carbon footprint of the produced glass.
As a result, we are now able to select locally sourced sand that would otherwise have been rejected for quality reasons and can thus reduce the transport. It also allows to decrease the processing actions by avoiding processes which are not mandatory to reach the ‘just good enough’ quality. Furthermore, there is less waste as sand fractions which would have otherwise been rejected, and can now be used, minimizing the total tonnage extracted and our impact on natural resources.
Reducing the environmental impact of transport
AGC Glass Europe takes actions in the field of raw materials transport with the objective to reduce its environmental impact. This involves :
- minimizing distance to supply (for example the local sourcing of sand, ..),
- maintaining or developing infrastructures in glass plants to receive mass transport such as barges and trains, access ways, unloading facilities and storages. Transport by ship or train causes less emissions of CO2, NOx, SOx and dust than transport by truck. It also helps reducing road congestion.
When truck transport is unavoidable, we minimize its environmental impact by not requesting dedicated trucks and thus minimizing the empty return percentage.
AGC Glass Europe has started discussion with all transport supplier (maritime, truck) to request for a monitoring of the CO2 emissions related to its shipments and collaborate to define best proposals (as example biodiesel (HVO) , electric truck) to decrease the global environmental footprint of the transport.
Selection of Soda Ash
Soda ash is the second largest raw material by volume but the first in terms of carbon impact. There are important differences in the carbon footprint of soda ash depending on the type of soda or process:
- synthetic Solvay process or natural trona,
- distant or local,
- from standard processes or processes improved to reduce their carbon footprint such as the use of biomass, renewable electricity, or efficient steam production.
The production of the recently launched Low-Carbon Glass range is based on soda ash that has a reduced carbon footprint.
Chemical Management and
compliance with REACH regulation
REACH Regulation has entered into force more than fifteen years ago and has developed continuously. It organizes the management of chemicals in the European Economic Area, to ensure a high level of protection of human health and the environment. REACH stands for Registration, Evaluation, Authorisation and restriction of CHemicals. It requires for example that chemical substances manufactured, imported, or used in Europe must be registered, gathering sufficient information for safe use. It requires also that information on substances must be communicated up and down the supply chain.
Registration & role of AGC Glass Europe as article producer
The final products that AGC Glass Europe puts on the market and supplies are not substances or mixtures, but articles. Articles are not entitled to be supplied together with a Safety Data Sheet, so this also applies to AGC Glass Europe products.
The glass itself, which is the basic constituent of AGC Glass Europe products, is exempted from registration following Annex V.11.
AGC Glass Europe is mainly a downstream user of substances and mixtures, in order to produce its own products. In this case, AGC Glass Europe ensures that its suppliers have registered their substances and are following REACH Regulation. From the beginning of REACH scope, AGC Glass Europe is discussing with its suppliers to ensure that AGC's uses and its customers' uses are considered and registered by its suppliers.
SVHC on the Candidate List for Authorisation, substances tracking and information in the supply chain.
AGC Glass Europe has a long-time policy of avoiding as much as possible the presence of dangerous substances in its products. However, if a SVHC in the Candidate List is present in a concentration above 0,1% w/w in an AGC Glass Europe product or in one of its parts (sub-article), AGC Glass Europe would provide the recipient of the product with all the relevant information pursuant to article 33.1 of REACH Regulation.
Also, if it would happen that the conditions of article 7.2 of REACH Regulation are met, AGC Glass Europe would notify the Agency accordingly.
Restrictions under REACH Regulation
Annex XVII of REACH Regulation contains the list of restricted substances, specifying which uses are restricted. AGC Glass Europe takes great care to comply with those restrictions, according to article 67.
More on our decarbonisation journey
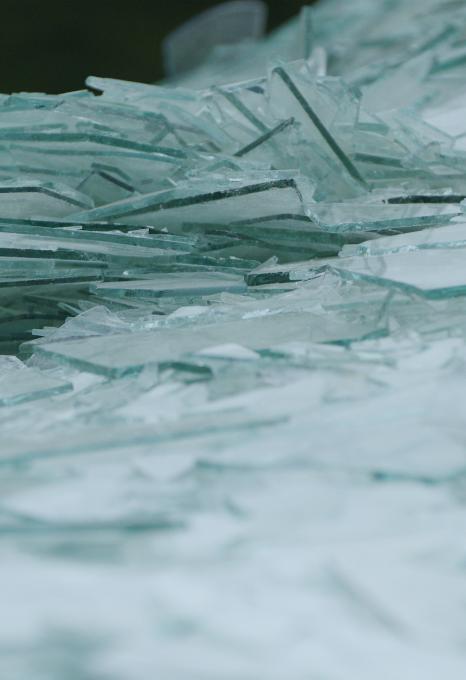
Increasing the use of cullet
Glass is endlessly recyclable like no other product. Our main objective is to use as much glass cullet as possible in our production processes. The use of cullet avoids CO2 emissions, since cullet requires less energy to melt, and replaces carbonated raw materials. Cullet is a key material to save natural resources and energy.
AGC Glass Europe to incorporate Eastman’s Saflex™ LiteCarbon™ Clear interlayer into Low-Carbon Stratobel Glass
The integration of Eastman's Saflex™ LiteCarbon™ Clear interlayer into AGC's Low-Carbon Stratobel Glass represents a significant step forward in reducing the embodied carbon of laminated glass products.