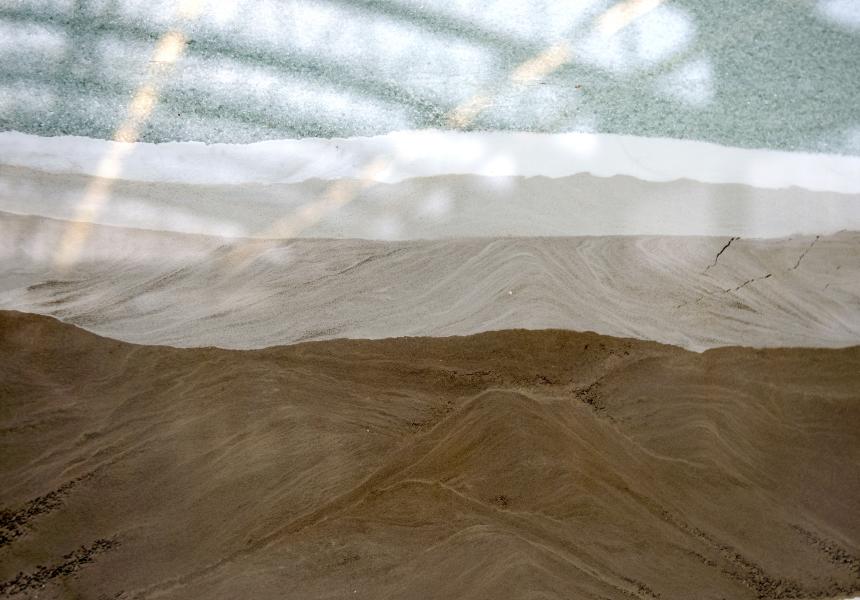
Sustainable sourcing of raw materials
The nature and type of raw materials used has a great impact on AGC’s CO2 emissions. The manufacturing processes of our suppliers are not equal regarding their CO2 emissions and, logistics can vary a lot. AGC has started discussions and onsite audits of the different suppliers to better understand their current situation and their plans, including logistics. This will impact the selection process of our suppliers. This CO2 dimension will come on top of aspects such as costs or quality specifications.
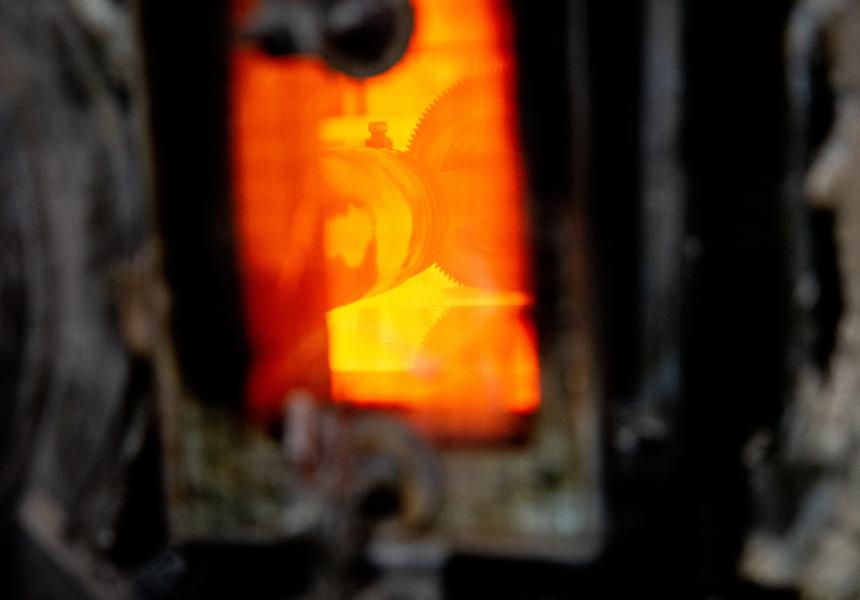
Using highly efficient melting furnaces
AGC is engaged in a major transformation of the tank technology. The industry standard is an air/gas combustion system. The two steps electrification innovation, electro-boosting and then hybrid melting, is a major technology breakthrough. Furthermore, additional efforts are done on the overall energy efficiency of our systems.
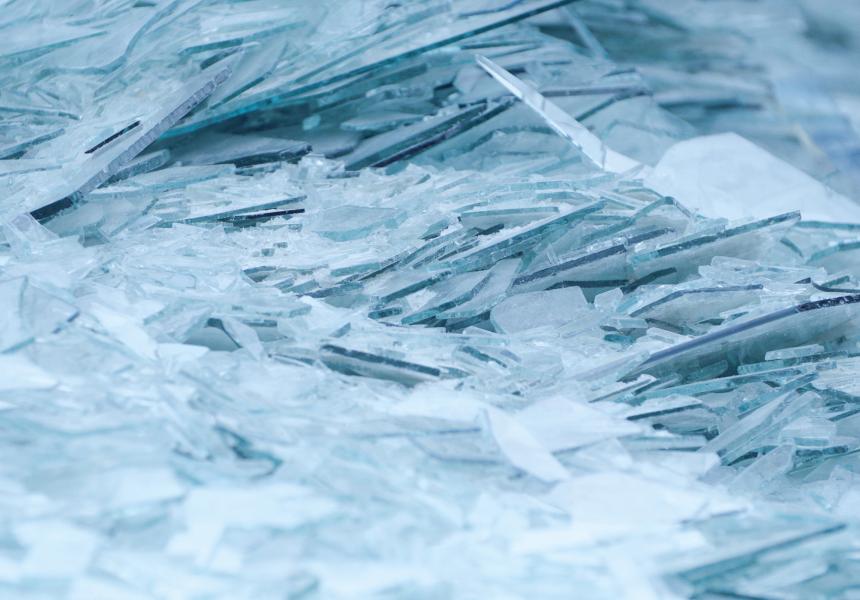
Increasing the use of cullet
Cullet is glass waste, it is glass that is not usable anymore. There is glass waste at the primary glass manufacturing plants, at our our customers plants, when manufacturing windows, and at the end of life, after a window renovation or once a building is demolished.
Glass can be re-melted indefinitely, and we know that 1 tonne of cullet allows to save 1.2 tonnes of raw materials. Cullet also lowers the energy need as the energy need is lower than with fresh raw materials.
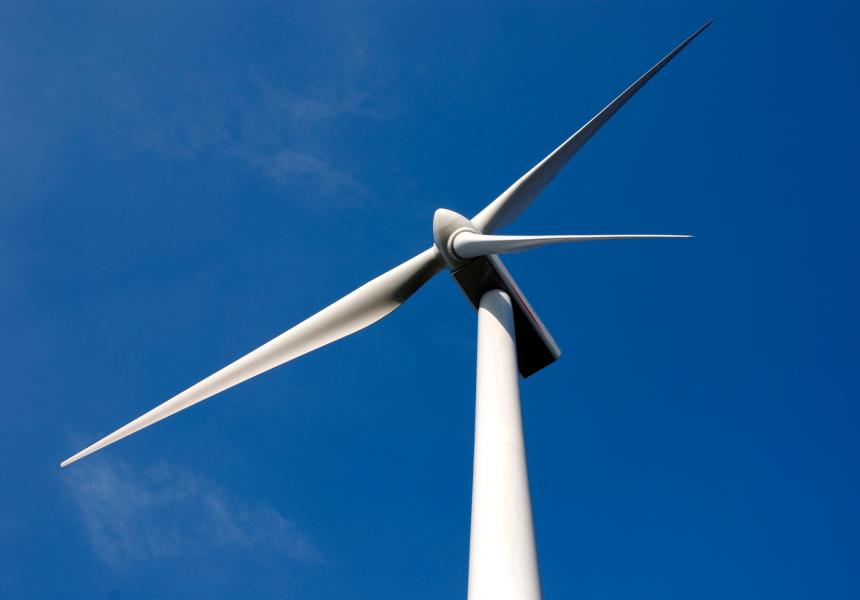
Using low carbon electricity
The electrification process will significantly increase the electricity consumption while reducing the fossil energy, as natural gas. It is then crucial that the emission factor of that electricity is low. This is called low carbon electricity. There are different ways to get this kind of energy: self-production via windmills or photovoltaic panels or specific contracts with energy producers, such as a PPA, a purchase power agreement.
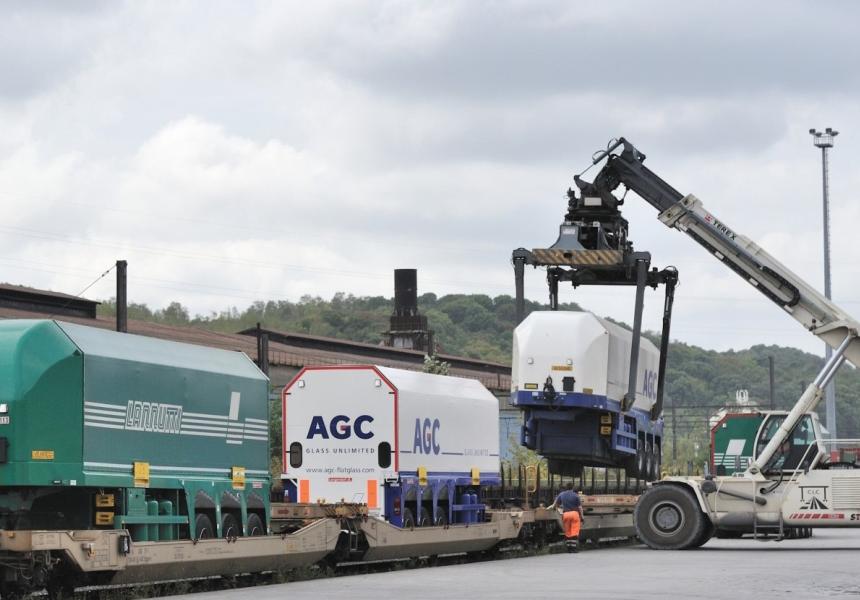
Optimising transport
For finishing processes. Float glass goes through a series of finishing processes before ending as a wide variety of finished products with added value. This requires multiple internal shipments from one manufacturing plant to another one, and has a considerable impact on our CO2 emissions. Over the last years we have reduced this internal footprint by minimizing useless transports and maximizing the number of finishing operations at one location.
For finished products. The shipments of finished products to our customers are also to be organized in an efficient way to minimize the carbon footprint. Interesting multimodal systems, combining trucks and trains, have been developed.